Is It Time to Upgrade Your Laundry Operation?
BY KIM SHADY |
Is it time to upgrade your laundry operation? Old, inefficient equipment can increase costs in an in-house laundry operation |
Clothes go out of style and grocery items come with expiration dates; however, it’s hard to know when a washer-extractor and other on-premise laundry equipment have surpassed their useful life spans. While there are no absolutes to determining when to upgrade laundry equipment, there certainly are signs to look for. In addition, administrators and laundry managers should equip themselves with the tools to make informed decisions about replacement products. Afflicted and Aged Frequent service calls may be leading up to the most serious of repairs-a bearing replacement. This is a problem that managers will hear coming; the machine will have a noticeably louder sound during operation. A costly repair, bearing replacement may run between $2,000 and $3,000. Managers should carefully weigh whether spending that sum on an machine that has been in service for more than eight years is a prudent expenditure. Most likely it is not. Look at the Workload Labor is the number one cost in a laundry operation. Any time a laundry room is operating for more than eight hours, a manager should look at ways to reduce hours. Managers who are seeing increases in overtime or who are considering adding a second shift to keep up with demand may first want to investigate how equipment upgrades will affect productivity. New, more efficient equipment might solve the problem. The Not-So-Hidden Costs With some older washer-extractors operating at extract speeds of just 86 g-force, upgrading to a new machine boasting super-high g-force of 300 could save an average-size operation between $1,200 and $1,500 per dryer, per year in natural gas charges. Such savings are rooted in the super-high extraction speed that removes far more water from linens. As a result, drying time, and ultimately gas use, goes down. The Next Step Obviously, the size and number of fill valves determines how quickly the machine reaches its wash level. While it may seem like a small component, extra time spent during this function for each cycle can add up to decreased productivity across an eight-hour shift. Likewise, spray rinses are significantly faster than the traditional bath-style rinse. Therefore, managers seeking to save time will benefit from washer-extractors with such a feature. Programmability enables managers to maximize the machine’s efficiency. With the employee turnover that many laundry operations experience, user-friendly controls are a must. This feature will trim the amount of time managers have to spend training new staff members. Price Versus Cost For example, a lower priced washer-extractor may utilize a lower g-force extraction and consume more water. Thus, with added utility costs coming into view, the cheaper machine actually may cost more to own. It’s important to note that if there’s a big difference in price between washer-extractors, there’s a reason. Either the performance isn’t the same or the machines aren’t equal. The Intangibles
The Final Answers With the right approach and careful study, laundry managers at long-term care facilities can ensure that their equipment upgrade helps achieve the goals of better productivity and lower operating costs. Kim Shady, national sales manager for UniMac, has worked in the commercial laundry industry for more than 18 years. Owned by Alliance Laundry Systems, UniMac offers an industrial line of on-premise laundry equipment designed for efficiency and durability. For more information, call (920) 748-3121 or visit www.uniwash.com. To send your comments to the author and editors, please e-mail shady0706@nursinghomesmagazine.com. |
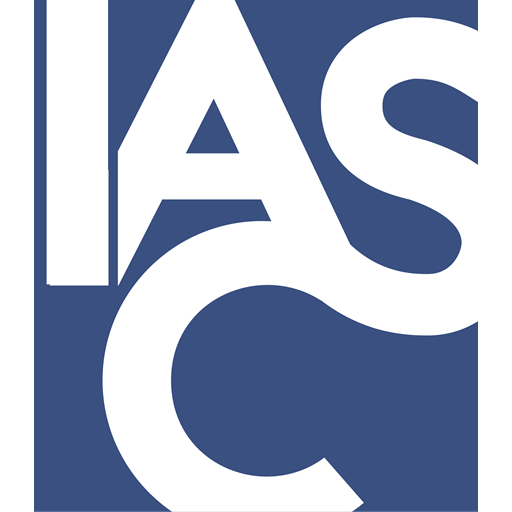
I Advance Senior Care is the industry-leading source for practical, in-depth, business-building, and resident care information for owners, executives, administrators, and directors of nursing at assisted living communities, skilled nursing facilities, post-acute facilities, and continuing care retirement communities. The I Advance Senior Care editorial team and industry experts provide market analysis, strategic direction, policy commentary, clinical best-practices, business management, and technology breakthroughs.
I Advance Senior Care is part of the Institute for the Advancement of Senior Care and published by Plain-English Health Care.
Related Articles
Topics: Articles , Operations