A manager’s guide to labor cost management
Labor is a provider’s largest expense, and one that historically has not been managed as well as it could and should be.
For many providers, reductions in agency staff and minimizing overtime are fast-track ways to control labor costs. You can experience even greater results by adding a third element of cost control: managing to your budget thresholds, as tightly as possible. Small variances in budgeted labor versus actual labor can add up to tremendous savings over the course of a year.
Many providers do a very good job reducing their agency usage or eliminating it altogether. Overtime, however, is typically managed in a reactive way and small differences between the labor budget and what is actually scheduled are difficult to identify. For organizations that manage staff schedules with pen and paper, these differences, which can yield significant savings, become invisible.
A keen eye toward preventing overtime and proactively managing the gap between scheduled hours and budgeted hours will go a long way to improving your bottom line. With a few key practices, you’ll see how modest improvements in these areas can produce significant and noticeable financial results without sacrificing care.
OVERTIME INSIDE AND OUT
Let’s explore overtime to pinpoint how and where improvements can be made to lower labor costs. There are three core types of overtime:
Scheduled overtime-often a result of short-staffing.
Incremental overtime-occurs when full-time staff punch-in early or punch-out late.
Frictional overtime-due to staffing emergencies like call-offs, no-shows or terminations.
SCHEDULED OVERTIME
While “scheduled” overtime may be somewhat of an anomaly, it’s an extremely common practice in facilities today. The good news? It can be prevented, without understaffing. Get started by giving schedulers more visibility into hours worked, by employee. As a new monthly or weekly schedule is produced, make sure the scheduler calculates daily and weekly totals for each employee. If an employee is scheduled for overtime at the start of a pay period, take the time to find out why. There can be myriad reasons why scheduled overtime occurs:
Are you short-staffed and unable to cover shifts without overtime?
Was someone promised overtime when they were hired?
Is the scheduled overtime an oversight?
Be sure to evaluate and understand the reasoning behind each instance of scheduled overtime. Minimize scheduled overtime by establishing a policy against it without receiving approval from the DON or administrator. With these controls in place, you will quickly see that scheduled overtime can be prevented.
INCREMENTAL OVERTIME
Incremental overtime is a common source of excess labor costs, but it is often the least visible. Get your arms around it with some additional reporting. Schedulers should produce a report at the start of each day identifying each employee’s scheduled time for the week, and how much time he or she has punched week-to-date (WTD). Add to this his or her remaining scheduled hours for the week. This report will highlight employees punching more than their scheduled hours and identify those projected to go into overtime (see table on p. 26).
In the example report depicted in the table, you can clearly see that Mary and Mike are punching more time than they are scheduled. Both are going to earn overtime for the week (assuming a standard 40-hour rule). Get control over this situation by addressing it as soon as possible. When you see a discrepancy, question the employee or his or her supervisor to find out if the extra time was spent providing care. Find out if it was approved or unapproved. Once employees are aware that you are paying close attention, incremental overtime will naturally decrease.
FRICTONAL OVERTIME
Frictional overtime is the most difficult to manage. You may have a perfect schedule that’s closely correlated to your census, but then a nurse calls in sick and a CNA quits. Those shifts need to be filled quickly. This is when and where significant overtime risks begin.
It’s common for schedulers to start calling the people they know will pick up shifts in order to find a replacement as quickly as possible. This practice will frequently lead to overtime. Consider the example report in the table. With this report in hand, prioritize calls to those people who are not projected to be in overtime. Be sure to consider part-time staff to fill unexpected open shifts, and call part-timers first. In addition, establish a time threshold for filling the shift. For example, if the call-off is for a shift tomorrow morning, give the scheduler the majority of today to find the most suitable replacement. Consider the “go-to” list of people who will likely incur overtime as your backup plan, calling them only if necessary.
Once open shifts are distributed more evenly to a broader group of people, you will experience a boost in staff satisfaction. Unfair allocation of call-offs and open shifts is one of the most common complaints I hear from facility staff. With this new process that promotes fairness, you’ll see that staff members are happier.
Controlling all three types of overtime can produce fast and significant results. For example, just a 1 percent reduction in overtime for a 10-home chain with an average of 100 beds can save more than $300,000 per year.
LOOK FOR OPPORTUNITIES
In addition to the above overtime examples, opportunities exist to reduce costs by managing staff schedules more precisely correlated to your budget thresholds. When there is going to be a change in census either due to discharges or intakes, be sure to correlate your scheduled labor to the revised census. For example, if you have planned discharges for tomorrow, determine the number of full-time staff you need with this lower census. Compare this with the number of staff on your schedule. You may identify an opportunity to reduce a shift that is no longer necessary.
Review schedules regularly to see if you are in the right range. If not, dig deeper into the details. Do not miss the opportunity to cut unnecessary shifts. Preventing and reducing unnecessary shifts leads to significant savings. For example, cutting just two unnecessary shifts per week, one nurse and one CNA, can deliver more than $15,000 in savings per facility annually.
BUSINESS TECHNOLOGY
Finally, consider automation to assist your efforts to control labor costs by minimizing overtime and managing staffing more efficiently and accurately. Technologies are available today that automate processes such as scheduling, overtime control, balancing staffing levels and managing open shifts. Look for technologies that span systems to give you access to the information and data you need to make timely and informed decisions. Take advantage of opportunities to systematize manual efforts, especially those that drain valuable resources, result in cost overruns and ultimately take time away from care.
Labor management is a major part of your business, so be sure to continually look for areas to improve. These practices will not only help manage overtime to reduce costs, but also deliver additional benefits that may surprise you. Staff will gain more time for care. Staffing levels will more closely meet HPPD (hours per patient day) budgets and requirements. And turnover will decrease because staff members are happier. With these results, those who benefit most are your residents. Now that’s a key to success that’s tough for any LTC or senior living operator to pass up.
Mark Woodka is CEO of OnShift, a provider of Web-based staff scheduling and shift management software for long-term care and senior living. He may be reached by email at
mark@onshift.com. Long-Term Living 2011 August;60(8):24-26
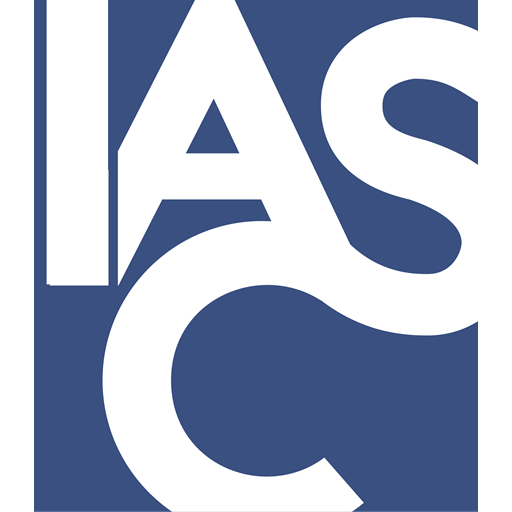
I Advance Senior Care is the industry-leading source for practical, in-depth, business-building, and resident care information for owners, executives, administrators, and directors of nursing at assisted living communities, skilled nursing facilities, post-acute facilities, and continuing care retirement communities. The I Advance Senior Care editorial team and industry experts provide market analysis, strategic direction, policy commentary, clinical best-practices, business management, and technology breakthroughs.
I Advance Senior Care is part of the Institute for the Advancement of Senior Care and published by Plain-English Health Care.
Related Articles
Topics: Articles , Staffing